Turbo Pumps for Liquid Rocket Engines
Although the word “turbopump” is not found in most dictionaries, Webster does define the prefix “turbo-“: “Turbo-” indicates turbine, or pertaining to, or driven by, a turbine; such as a turbo-jet, turbo-fan, or turbo-prop.” Turbopump is a compound word selected to describe the rotating machinery used to pump the liquid propellants in a rocket engine, and consists of one or more pumps driven by a turbine.
The function of the rocket engine turbopump is to receive the liquid propellants from the vehicle tanks at low pressure and supply them to the combustion chamber at the required flow rate and injection pressure. The energy to power the turbine itself is provided by the expansion of high pressure gases, which are usually mixtures of the propellants being pumped.
The liquid rocket engine turbopump is a unique piece of rotating machinery in comparison to turbo-jets, turbo-fans and turbo-props, since it is typically pumping cryogenic liquids while being driven by high temperature gases, posing large temperature differentials between the pump and turbine. The pump must avoid cavitation while pumping relatively high density fluids at low inlet pressures, and deliver them to the thrust chamber at very high pressures over a relatively wide throttling range. Typically, the turbine is driven by fuel-rich combustion products having available energy and heat capacity levels 10 times that of the typical turbo-jet. The turbopump is optimized for performance and weight within the minimum possible envelope size to facilitate engine packaging. Bearings normally operate in the propellants being pumped which have minimal lubrication characteristics. Static and dynamic seals are employed to preclude mixing of propellants within the turbopump which would result in burning and catastrophic failure.
The turbopump configuration is highly dependent on the engine cycle and the engine requirements for flow and pressure. Various turbopump configurations will be discussed at a conceptual design level, utilizing the disciplines involved in the design selection process, the “state of the art” of rotating machinery when each design took place, and the engine cycle requirements that influence the turbopump design.

A study in contrasts. During a test firing, the liquid propellant inlet section of this experimental turbopump is coated with ice, while the gas inlet from the combustion chamber glows red hot. Such as the working demands on turbopump technology.

The need for turbopumps is directly related to mission velocity and payload requirements.
Engine Requirements
Liquid rocket engines are either pressure-fed or pump-fed, depending on the mission requirements. If the mission velocity and payload are low, the propellants are fed to the thrust chamber by pressurizing the vehicle tanks. As the mission velocity requirement increases, the chamber pressure must be increased to raise the thrust from each pound of propellant in order to increase the vehicle thrust-to-weight ratio. This justifies the added complexity of the turbopumps to minimize the vehicle tank weight.
The type of engine cycle selected also influences the turbopump requirements and configuration. Generally, three types of engine cycles have been used in liquid rocket engines: the gas generator cycle, the staged combustion cycle and the expander cycle. The engine cycle terminology refers to the source of energy to drive the turbine.
Gas Generator Cycle
In a gas generator cycle engine, the turbine flow is in parallel with the thrust chamber and is not used to develop thrust. Sufficient propellants to drive the turbine are removed from the pump discharge, combusted in the gas generator, and expanded through the turbine to atmospheric pressure. The required pump discharge pressure is established by the combustion chamber injection pressure and establishes the available pressure to drive the turbine. Hence, the required pump flow rate is equal to the combustion chamber flow plus the flow required to drive the turbine. With the turbine discharging to atmosphere, the available energy per pound of flow is large due to the large pressure ratio. Maximizing the turbopump efficiency and increasing the turbine operating temperature to the available material limits reduces the required turbine flow rate while increasing the engine specific impulse per second (thrust per pound of propellant used). Turbine temperature is generally selecte d based on a trade study of engine weight, turbine design complexity and specific impulse. Gas generator cycle engines, therefore, minimize the pump-required discharge pressures, maximize the pump-required flow rate and maximize the turbine operating temperature for a given combustion chamber pressure. Prior gas generator cycle engines built by Rocketdyne (now Rocketdyne Propulsion and Power, a part of The Boeing Company) included the Redstone, Thor, Jupiter, H-l, F-l, and the J-2. Current active gas generator cycle engines built by Rocketdyne include the Atlas, RS-27, and the XLR-132.
Staged Combustion Cycle
In the staged combustion cycle engine, the turbine flow is in series with the thrust chamber. Most of the fuel flow and enough of the oxidizer flow to accomplish the desired turbine temperature are removed from the pump discharge, combusted in a preburner, and expanded through the turbine to the combustion chamber injection pressure. The remainder of the oxidizer flow is added in the main combustion chamber to complete the combustion process. A staged combustion cycle engine maximizes the engine’s specific impulse by passing the turbine flow through the thrust chamber to develop thrust. This does, however, raise the turbine discharge pressure to a value in excess of the main combustion chamber injection pressure. The turbine power required to drive the pumps determines the required turbine inlet pressure and the required pump discharge pressures; pump flow rates are equal to the thrust chamber flow rates. Maximum turbopump efficiencies and maximum turbine temperatures minimiz e the required turbine inlet pressure and pump discharge pressures and, therefore, minimize the turbopump weight. A tradeoff between turbine temperature and pump discharge pressure is normally made to establish the turbopump requirements. The staged combustion engine, therefore, maximizes the pump discharge pressures, minimizes the pump flow rates and maximizes the turbine operating temperature. The Space Shuttle Main Engine (SSME) is a staged combustion cycle engine.

Three common engine types. Red denotes fuel flow, while green denotes oxidizer flow.

Expander Cycle
In the expander cycle engine, the turbine flow is also in series with the thrust chamber. However, the turbine available energy is limited only to the fuel flow which is preheated in the thrust chamber coolant passages instead of being combusted with liquid oxygen in the preburner. The expander cycle engine also maximizes the engine’s specific impulse for a given chamber pressure by passing all the propellants through the thrust chamber. The pump-required discharge pressure is equal to the thrust chamber injection pressure plus the turbine pressure drop. Energy available to drive the turbine limits the expander cycle engine to relatively low thrust chamber combustion pressures, moderate pump discharge pressures, and low turbine operating temperatures. The cryogenic Orbital Transfer Vehicle engine is an expander cycle engine.
Other Engine Factors
Other engine factors that significantly influence the turbopump configuration selection are the types of propellants, the propellant inlet conditions and the engine throttling requirements. Typical propellants include RP-1, LH2, LO2, MMH, NTO, and other liquids with wide density ranges and temperatures. The variations in density produce significantly different pump head rise (pressure) requirements and large differences in volumetric flow, i.e., low density propellants require a much higher head rise to develop the same discharge pressure (head rise=pressure rise/density, DH=DP/p). The variations in the combined propellant available energy have a significant influence on the turbine design.
The propellant inlet condition, which is expressed as the pump-inlet net positive suction pressure (NPSP=propellant inlet total pressure-propellant vapor pressure), dictates the pump’s suction performance requirements, The pump suction performance requirement is its ability to operate at the available NPSP without detrimental cavitation.
The engine throttling requirements define the range of flow and discharge pressure that the turbopump must deliver with stable operation. The engine start and shutdown characteristics must also be considered to prevent unstable turbopump operation due to cavitation or stall.
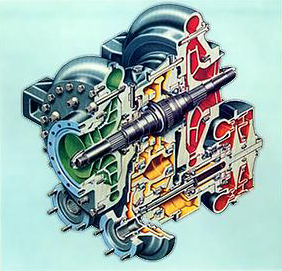

The SSME HPF turbopump

The Mark 49F, used in the OTV

The Mark 15F, used with the J-2.
Configuration Selection
With the engine requirements established, the turbopump configuration is selected based on optimizing the pumps for each propellant, the turbine for the drive gas available energy, and the mechanical design arrangement for life, weight and producibility considerations.
Pumps for engines with similar density fuel and oxidizer propellants such as RP-1/LOX and similar discharge pressure requirements will typically be optimum at approximately the same speed. This permits the fuel and oxidizer pumps to be placed on a common shaft and driven by a common turbine (Redstone, Atlas, RS-27, F-1, and XLR-132). Maximum pump speed is generally limited by the suction performance requirements to avoid cavitation. Optimum turbine efficiency requires a certain pitchline velocity which is a product of the shaft speed and the turbine diameter. The minimum weight turbine has the highest speed and smallest diameter within the structural and mechanical arrangement limitations.
When the Atlas booster and sustainer turbopumps were designed, the speed of the pumps and the turbine were optimized independently and linked together with a speed reduction gear box, This required the development of a highly loaded gear train to minimize the turbopump weight, but was considered the best design selection based on suction performance, turbine performance and material technology at that time.
When the F-1 turbopump was designed, canted inducer technology had been developed to increase the pump suction performance capability. This permitted designing the pumps and turbine to operate at the same speed on a common shaft and eliminated the need for a 60,000-hp reduction gearbox, which was probably not feasible anyhow.
The J-2 was the first gas generator cycle engine to use liquid hydrogen (LH2) as the fuel and liquid oxygen (O2) as the oxidizer. The low-density liquid hydrogen introduced the need to operate the fuel pump at a much higher speed than the LO2 pump in order to develop the high head required. High solidity inducer technology had been developed which permitted optimizing the LH2 pump at a higher speed and driving the pumps with separate turbines. The turbines were arranged in series to best utilize the large pressure ratio available energy and maximize the turbine efficiencies at their respective speeds.
Selecting a 3,000-psi chamber pressure and staged combustion cycle for the SSME to maximize the specific impulse significantly increased the turbopump requirements compared to the F-1 or J-2 engines. Adding preburner and turbine pressure drops in series with the high combustion chamber pressure resulted in discharge pressure requirements of 8,500 psia and 7,000 psia for the LO2 and LH2 pumps, respectively.
Propellant tank pressures were also minimized to optimize the Space Shuttle vehicle weight. The combination of low inlet pressures (low NPSP) and high required discharge pressures introduced the need for separate boost pumps to optimize the turbomachinery weight. The low pressure fuel turbopump and low pressure oxidizer turbopump receive the propellants at low NPSP and raise their pressures sufficiently to optimize the high pressure fuel and oxidizer turbopumps at high speed. The added complexity of four turbopumps is justified to optimize the turbomachinery weight and maintain suction performance margin for safe engine operation. The combination of high pump discharge pressure and flow requirements, combined with high horsepower turbines driven by high-pressure hydrogen-rich steam, have made the SSME turbopumps a significant advancement in the state of the art for rocket engine turbomachinery.
Pumps
Pump configuration is based on the requirements derived from the engine system. Inlet conditions (NPSP), discharge pressure, flow rate, and operating range must all be satisfied. A parametric analysis is performed to select the best speed, diameter and number of stages compatible with the turbine and mechanical design considerations.
The pump inlet diameter is generally selected based on the available NPSP. Test experience has been accumulated on inducers to correlate their suction performance as a function of the NPSP (generally expressed as NPSH), the fluid inlet meridional velocity (Cm), and the inducer flow coefficient (f).
The inducer diameter (inlet area) is selected to limit the fluid meridional velocity (Cm) so that the available NPSH/Cm2 /2g is equal to or greater than 3 velocity heads for water, 2 for LO2 and 1 for LH2 . Variation in the empirical limit accounts for the difference in thermodynamic suppression head between water, LO2 and LH2. As the available inlet pressure and NPSH are decreased, the inducer diameter must be increased in order to decrease the fluid velocity (cm) and maintain NPSH/cm2/2g equal to the velocity head limit. The limit is also a function of the inducer flow coefficient, which is defined as the meridional velocity divided by the inducer tip speed:

With the inlet diameter selected, the shaft speed is selected to limit the inducer tip speed to approximately 550 ft/sec. The tip speed limit is for controlling the tip vortex cavitation energy, which is a function of tip speed to the sixth power. The blade thickness must also increase with increased tip speeds to react the centrifugal and pressure loading. This reduces the flow passage area and, therefore, lowers the suction performance. The pump suction specific speed is expressed as

This is a measure of the pump’s ability to operate at low inlet head (NPSH) without cavitation (formation of vapor bubbles) sufficient to cause head loss. A 50% NPSH margin is generally selected during the design process for long-life rocket engine applications. Cavitation, in addition to decreasing the pump discharge pressure and efficiency due to the formation of vapor bubbles, can cause significant structural damage when the vapor bubbles collapse (implode), particularly with high-density fluids. Rocketdyne’s inducer technology development has been a key state-of-the art advancement for increasing the pump speed, decreasing the turbopump weight and increasing the safe operating life. The double entry back-to-back pump was selected for the HPOTP in the SSME in order to increase the shaft speed by Ö2 and stay within the tip speed limit, while maintaining the required total inlet flow area.
Required pump head, which is a function of the required discharge pressure, the available inlet pressure, and the propellant density [DH=(Pd – P in.) / r], is the major factor in selecting the pump configuration. The head coefficient (y=DH / U2 /g) is a function of the pump type and establishes the required pumping element diameter and number of stages to develop the required pump head for a given shaft speed. The main pumping element may be a centrifugal, mixed, or axial flow type.

Turbine efficiency is shown as a function of blade velocity and gas spouting velocity ratios

Suction performance improves over a 40 year period.
A convenient parameter which reflects the difference in pump geometry characteristics is the specific speed which is a function of the shaft speed, volumetric flow, and required headrise:



Pump Types. top to bottom: inducer, high specific speed;
axial, intermediate specific speed; centrifugal low specific speed.
Low specific speed pumps are typically centrifugal with head coefficients (y) ranging from 0.4 to 0.7, which is a function of the impeller blade discharge angle. Intermediate specific speed pumps are typically mixed or axial flow with head coefficients, y, ranging from 0.4 to 0.2 per stage; and high specific speed pumps require only an inducer to generate the required head.
The head requirements for high-density fluids such as RP-1 and LO2 can be generated with a single stage centrifugal pump, with the impeller diameter well within aluminum and nickel-base alloy steel structural limits. Head requirements for low-density fluids such as LH2 are very high and typically require several stages to develop. An axial flow main pumping element was selected for the J-2 LH2 pump because of its intermediate specific speed and narrow throttling range requirements. The 200,000-foot head requirement for the SSME HPFTP dictated a three-stage centrifugal pump with the impellers operating at 2,000 ft/sec tip speed. Titanium, which has a higher strength- to-weight ratio than the high-strength nickel-base alloys, was required for the high tip speed.
Optimizing the pump efficiency, which is a measure of the work-out/work-in, can also influence the shaft speed and specific speed selected. Maximum pump efficiency can generally be developed in the 2,000 to 3,000 specific speed range. Small flow rate pumps are generally less efficient than large flow rare pumps because the clearance and surface finish related losses cannot be scaled with size.
Turbines
The turbine must supply the required power to drive the pump utilizing the drive gas provided by the selected engine cycle. Overall performance of the turbine depends upon three variables: the available energy content per pound of drive gas, the blade tangential velocity (U), and the number of turbine stages. The available energy for the turbine pressure ratio can be expressed as an ideal velocity, C. The turbine velocity ratio, U / C, is used to empirically characterize these two variables versus the turbine efficiency.
The ideal velocity can be distributed between the turbine stages with either a pressure- compounded or velocity-compounded design. The major difference between these two turbine designs is where expansion occurs in the stationary blade rows. For the velocity-compounded turbine, all the expansion occurs in the first stationary blade row, while for a pressure compounded turbine, the expansion is distributed between the stationary blade rows. For high U/C designs, the turbine efficiency can be further improved by having some of the expansion (reaction) take place in the rotor blades. The design selection is made to maximize the turbine efficiency and minimize the weight compatible with the selected shaft speed. In general, when a direct drive turbopump configuration is selected, the shaft speed is less than optimum for the turbine and additional stages must be added to utilize the available energy.
Blade tip diameter is selected to optimize the U/C for efficiency within the blade height-to- diameter performance limits and within the tip speed structural limits. If the blade height- to-diameter ratio gets too small, the tip clearance and secondary flow losses become large, decreasing the turbine efficiency. The tip speed structural limit is based on the centrifugal pull that can be carried at the base of the blade airfoil for the selected material and is generally expressed as allowable annulus area x N2 versus temperature. Partial admission turbines are selected when the shaft speed is too slow and the blade height-to-diameter ratio becomes too small to obtain the desired U/C. The blade diameter is increased to increase U and the arc of admission is decreased to maintain the blade height at an acceptable height-to-diameter ratio.
Mechanical Design
Turbopump mechanical design is a compatible compromise involving many contributing factors, including power transmission, rotordynamics, axial thrust balance, bearings, dynamic seals and thermal considerations.
The shaft diameters, splines, and couplings must all be large enough to transfer the torque, which is a function of speed and horsepower. This establishes the shaft diameters and the bearing inner race minimum allowable diameter, depending on the axial stations selected along the shaft. The rotor critical speeds are a function of the rotor mass distribution and spring rate, the bearing locations and spring rate, and the housing stiffness. For rolling element bearings, the product of the inner diameter and the shaft speed (DN) is used as a measure of the bearing internal loading. Empirical life limits have been established for DN as a function of the propellant or lubricant used to cool the bearing.
With these interacting limitations, the bearing locations are selected to keep the operating speed range clear of critical speeds and minimize the bearing bore diameter to maximize bearing life.
From a critical speed standpoint, inboard bearings decrease the bearing span and increase the first critical speed so long as the overhang does not exceed approximately one-half the span length. However, this means that the power torque must pass through the bearing bore which maximizes the bearing diameter and DN when the bearing is placed between the pump and turbine.

In this series demonstrating the effects of cavitation note the gradual formation of small bubbles as inlet pressure (NPSH) is decreased. These eventually implode, causing damage
to the turbine metal. The final photograph indicates the severity of the effect.
From a bearing standpoint, the most desirable location is outboard so that the bearing size and geometry can be optimized independent of the required shaft diameter. However, bearings outboard of the pump inlet tend to decrease the NPSP available at the inducer due to the inlet losses, and also increase the inducer hub diameter, which in turn increases the outer diameter to maintain the flow area. Bearings outboard of the turbine generally require additional cooling, dynamic seals and support structure, which add complexity to the turbopump design.
Dynamic shaft seals to contain and separate the propellants and turbine drive gas must also be compatible with the shaft diameter and operating speed. LO2 seals, plus hot gas seals, plus intermediate seals purged with helium to separate the LO2 and hot gas leakage drains have to be placed between the pump and turbine on a LO2 turbopump with a common shaft. The seal package significantly increases the overhang for an inboard bearing cooled with LO2, which then lowers the rotor critical speeds.
Rotor stability is also a major factor in selecting the bearing locations and types of dynamic seals. Additional support stiffness and damping can be provided by the dynamic seals to raise the critical speeds and stabilize the rotor to prevent subsynchronous whirl. The HPFTP for the SSME has outboard bearings with a large bearing-span-to-rotor-stiffness ratio. Added support stiffness provided by the pump interstage seals raise the rotor first critical speed to greater than one-half the maximum operating speed which prevents subsynchronous whirl. The added damping by the interstage seals also permits operation at the second critical speed without significant rotor vibration.
The bearings for the Redstone, Atlas, RS-27 and F-1 turbopumps were separated from the pump cavities and lubricated with oil or RP-1, plus an additive. This mechanical arrangement, although optimum for bearing lubrication, required additional dynamic seals. The bearings for the J-2, SSME and OTV turbopumps are cooled with LO2 or LH2, eliminating the need for dynamic seals to isolate the bearings from the pump. This is a significant weight savings, but requires a departure from conventional oil- lubricated bearing design practices. The bearing races and balls are made of 440C material to prevent corrosion. The cage (separator) is made of Armalon, which is a glass-filled Teflon, to prevent metal-to-metal impact and provide a lubrication transfer to the balls and races.
The rotor axial thrust is the other major factor that influences the bearing design. The labyrinth seal diameters in the pumps and turbine are selected to minimize the net rotor thrust that must be reacted by the bearings. The pumps for the Atlas, RS-27 and F-1 are arranged back-to-back so that the thrust unbalance that must be reacted by the bearings are minimized.
With improvements in suction performance, higher operating speeds and smaller bearings, an active balance piston was introduced to react the rotor thrust. Orifices sensitive to the axial position regulate the pressure over an area of the rotor sufficient to balance the axial thrust. A separate disc was utilized in the J-2 LH2 turbopump for a double-acting balance piston. The back-to-back double-entry main impeller is utilized as the balance piston in the SSME HPOTP, while the third-stage impeller is utilized as the balance piston in the SSME HPFTP. Duplex pairs of preloaded angular contact ball bearings that float axially permit the balance piston to function in these turbopumps.
The development of hydrostatic bearings to center the rotor raises the DN limit associated with rolling contact bearings and increases the turbopump life potential. Hydrodynamic lift-off seals are also being developed to eliminate the life limits of face-riding seals. The combination of these two technologies removes some of the interactive constraints in the mechanical design selection process.
The rocket engine turbopump, in addition to being a high energy/weight ratio machine, must be designed to operate with the pump at cryogenic conditions and the turbine at high temperature. This requires design concepts that provide thermal growth flexibility while reacting large torques, separating loads and external ducting loads. Radial pins, axial cylinders and curvic couplings are typically used to perform this function.

Materials
Aluminum alloys, stainless steels, high strength steels, nickel base alloys, cobalt base alloys and titanium alloys are all used in the design of turbomachinery.
Complex pressure vessels for applications of up to approximately 2,000 psia are typically cast of aluminum to utilize its high strength-to-weight ratio and to avoid weld joints. Nickel-base superalloys such as Inco 718 are used to cast pressure vessels where higher strength is required. The high strength-to-weight ratio of titanium is utilized to obtain the high tip speeds required for LH2 impellers and inducers.
Hydrogen environment embrittlement effects of gaseous hydrogen limit the materials selected for turbine components. High-strength superalloys typically must be protected from the environment by copper or gold plating. Turbine blades are directionally solidified and thermally coated to survive heat fluxes ten times the typical turbojet and blade loads of up to 600 hp per blade.
Silver and Kel-F are used in LO2 pumps where contact with the inducer or impeller could result in ignition due to local heat generation. These materials are also used for potential contact with titanium impellers to preclude the formation of titanium hydrides due to heat generation.
The State of the Art
Turbopumps for liquid rocket engines are designed for maximum performance and minimum weight. Their operating environment includes extreme temperature and pressure ranges, rapid starts and exposure to propellants with unusual characteristics. The advancement in the state of the art of rocket engine turbomachinery over the past 35 years has been driven by lower inlet pressures to decrease vehicle tank weight, the use of LH2 as a fuel to increase the engine specific impulse, stage combustion cycle engines with higher chamber pressures to increase specific impulse and the need for throttleable, reusable engines. Space application engines with high chamber pressures and low flow rates are requiring small turbopumps with operating speeds in excess of 200,000 rpm.
The continued advancement in the state of the art of rotating machinery will be highly dependent on bearing and dynamic seal technology, Fabrication methods, material development, and a better understanding of the dynamic flow conditions within the turbopump through the development of three-dimensional computational fluid dynamics and special instrumentation.
Note: This article is a reproduction of the Boeing Engineering at http://www.engineeringatboeing.com/, written by M.L.”Joe” Stangeland